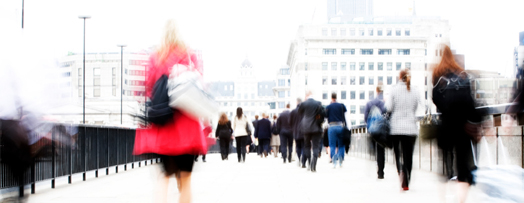
Process Improvement Advice & Best Practices
Understanding Theory of Constraints Basics
For everyone that has been involved in Continuous Improvement for the past twenty years, we have seen many new acronyms or abbreviations come and go. Methods like TQM, BPR, Lean, Six Sigma and TOC are just some of the many. At NOVACES, we have developed a comprehensive deployment methodology known as SystemCPI. SystemCPI is comprised of three important methodologies… Lean, Six Sigma and the Theory of Constraints (TOC). Of the three, TOC seems to be the most difficult for most people to grasp. What I have witnessed in the past few years is that consultants attempt to deliver excessively detailed explanations of TOC including the TOC Thinking Process (TP) tools. Typically the people on the receiving end of these explanations walk away feeling confused and bewildered. I know because I was one of those consultants who ended up confusing people. Several years ago I came up with a simple way of presenting TOC without confusing everyone in the audience. I’ve used this approach for all levels of organizations ranging from Mechanics to Army Generals and they all seem to “get it” when I keep the explanation simple. So how do I keep such an apparently confusing subject simple? What did I change to add simplicity to this subject?
Figure 1
I start by presenting Figure 1 which I explain to be a cross section of a simple piping system used to deliver water from Section A through Section G. I then ask the audience this question, “If you wanted to increase the throughput of water through this system, what would you do?” Almost everyone in the audience tells me to increase the diameter of the pipe in Section C. I then say, “Why C….why not Section D of E?” Almost everyone says that it’s the bottleneck. Then I ask them, “OK, how do you know how much bigger to make it?” Invariably someone in the audience responds by saying, “That would depend upon how much more water you need.” So right away I have the concept of constraints in their mind.
I then flash up Figure 2, which is a simple 4-Step process for making some kind of product complete with processing times for each step. I then ask, “So if you wanted to increase the throughput of product through this process, what would you do or how would you do it?” There’s usually a slight pause before someone says, “You have to speed up Step 2 because it’s the bottleneck in the process.” I then say, “Why not Step 1?” “Or how about Steps 3 or 4?”
Figure 2
Usually a good percentage of the audience will say, “The only way to get more throughput is to make the bottleneck go faster.” I then ask them, How would you know how much faster to make Step 2 go?” Someone in the audience, remembering the answer to the same question I asked about the piping diagram will say, “It depends on how much more throughput you need.” My final question is, “What happens to this process if you run Step 1 as fast as you can?” Someone in the audience always says, “You’d just stack up inventory in front of Step 2.” In this simple Q & A using these two simple diagrams you have just presented the basics of TOC.
We then discuss Goldratt’s 5 Focusing Steps and they see that they have, in fact completed Goldratt’s first three steps.
Step 1: Identify the System Constraint
Step 2: Decide how to exploit the system constraint
Step 3: Subordinate everything to the constraint
Of course we talk in more detail about things like applying Lean and Six Sigma to only the constraint (i.e. exploiting it); Subordinating non-constraints to constraints and why this method always works so well. That’s it….a simple and straight-forward way to introduce the basics of both TOC and SystemCPI.