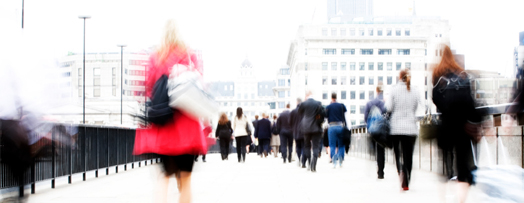
Process Improvement Advice & Best Practices
Higher Parts Availability With Less Inventory: A Case Study at Turkish Airlines Technic
Recently Dynamic Replenishment principles were successfully applied to Turkish Airlines Technic’s aircraft parts inventory system. The inventory, in this case, supported its maintenance and repair function, which is of vital significance to its operations in addition to maintaining third party aircraft. The aircraft on the line were either company owned or contracted from other airlines. Production tasks consisted of both periodic maintenance and the correction of operational malfunctions. The inventory system managed consumable items and rotable pools of subassemblies for both types of repairs. Initially, the purchasing system supporting replenishment was the Min/Max type.
The key difference between Dynamic Replenishment and conventional approaches is that it is fundamentally a ‘pull system’ rather than a ‘push’ system. A pull system controls the flow of supplies by automatically adjusting inventory levels based on actual consumption, with strategic buffers of inventory for each item to act as shock absorbers, compressing when inventory is consumed until replenishment occurs.
The existing inventory system was sometimes unable to provide parts to meet maintenance demand. Low parts availability may affect the cycle time to repair and deliver aircraft. Long cycle times represented lost opportunities: loss of passenger revenue for the additional time that the company owned aircraft were down for maintenance, loss of potential external revenue from additional external aircraft maintenance and repairs that could be conducted with excess capacity, and loss of premium payments from from external customers for quick turnaround of repairs.
Turkish Technic was determined to improve cycle times and commenced analysis of their inventory system under the initial subjective conclusion that variation in supplier replenishment times for required repair parts was one of the major contributors to stock out conditions and that waiting for parts in stock out condition was the biggest component of long maintenance and repair lead times. For the first phase of DR implementation, 1010 line items were selected from the 45,000 inventory items. These selected items were of high dollar value and had high consumption. The overall availability of these 1010 line items was 90.4% at the outset.
The general objective was to increase parts availability and reduce inventory. Analysis verified that wait time for parts out of stock was a significant nonproductive contributor to maintenance cycle time. However, the internal contribution to the replenishment lead time was larger than expected. The preliminary improvement phases were focused on ordering procedures for consumable inventory, deferring rotable demand to later phases of the improvement effort. Three critical actions were initially undertaken: establishing an internal pull replenishment system, maintaining targeted buffer inventory levels, and establishing supplier contracts and procedures consistent with DR system requirements.
Establishing an internal pull replenishment system included setting the order frequency of each line item to weekly. Decreasing these ordering frequencies resulted in an immediate reduction in inventory levels. Shipments were combined to avoid increases in transportation costs. IDEA’s Elucidate software was used to augment legacy inventory software. Elucidate automatically adapts targeted inventory levels based on changes in actual demand. The basics of an integrated automated ordering application were developed with the intention to connect the system directly to the suppliers in order to easily manage three times more orders. This ordering application might be implemented after the new ERP system is ready to use.
Maintaining targeted buffer inventory levels included several activities:
1) Dynamic buffer management,
2) Improvement efforts continued to reduce replenishment times,
3) Suppliers were assisted in expediting orders for line items with low on-hand levels, expediting decisions considered whether inbound orders were likely to arrive before stock out conditions occurred.
Establishing supplier contracts and procedures consistent with DR system requirements included communication with suppliers to make them aware of new ordering procedures and new expedite procedures. One prototype supplier was engaged to reduce their replenishment time. Contracts were modified for blanket purchase orders with longer terms, with smaller orders and with timely orders shipped to meet consumption. Transportation was managed to change the mix of parts being shipped to maintain full-truckload shipping.
In addition to supplier cycle time delays, one purchasing policy contributed significantly to lengthening replenishment lead time. For many orders placed, purchasing was required to research whether lower cost suppliers existed for the specific line item in the order. If a lower price could be found, the order was frequently shifted to the lower price supplier, to often one with longer replenishment times. In addition, the corresponding administrative delay due to the changing of purchasing contracts contributed to the internal component of the replenishment lead time. This policy, although based on cost savings motivation, frequently resulted in a negative impact on product throughput and drove AOG (aircraft on ground) emergencies. Delays resulting from this policy may have offset any cost benefit, since more inventory had to be held to cover the extended replenishment interval.
Now identified as a major contributor to replenishment lead time, re-engineering the price check activity to decouple it from the ordering procedure is being explored so that needed line items could be ordered without delay. In a future state, price checks will be conducted routinely, but apart from the ordering process to ensure cost savings. Changes to replenishment lead time due to changes in suppliers may be planned into future buffer modifications.
Only four months after the start of the second phase of DR implementation, initial purchasing process changes had been made and inventory data were collected. Overall availability had improved from 90.4% to 95.9% with $1.5 million less investment in inventory despite that fact that only a portion of DR Strategy and Tactics has been implemented so far. These gains resulted from the application of simple changes to inventory policies. The continued application of DR methods is projected to reduce replenishment lead times even further. Automated ordering and careful buffer management will continue to reduce stock out conditions and to reduce the cost of total inventory.