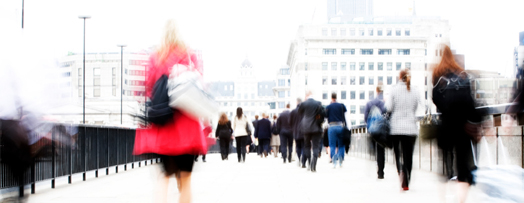
Process Improvement Advice & Best Practices
The key to sustaining change is FOCUS
I want to talk about the current state of Lean, Six Sigma and Lean Six Sigma initiatives as it relates to sustainment. The Lean Enterprise Institute (LEI) conducts annual surveys on the subject of how well Lean implementations are going. Considering the last three surveys (2004, 2005, and 2006), the results do not paint a rosy picture. In fact, LEI reported in 2004 that 36 percent of companies attempting to implement Lean were backsliding to their old ways of working. In 2005, the percentage of companies reporting backsliding had risen to almost 48 percent, while in 2006, the percentage was at 47 percent. With nearly 50 percent of companies reporting backsliding, we are not looking at a very healthy trend, especially when you consider the amount of money invested in the initiative. Add to this what Jason Premo of the Institute of Industrial Engineers reports: “A recent survey provided some shocking results, stating that over 40% of Lean Manufacturing initiatives have hit a plateau and are even backsliding, while only 5 percent of manufacturers have truly achieved the results expected.” And finally in 2010 research by McKinsey & Co. showed that 70% of all changes in organizations fail!
Okay, so if Lean and Six Sigma aren’t working well enough, then what do I recommend should replace them? The fact is, we shouldn’t replace them at all!! They are vital to the success of all improvement initiatives. What is missing is the necessary focus needed to maximize your return on your improvement investment.
By focusing the Lean and Six Sigma principles, tools, and techniques on the operation that is limiting throughput, your profits will accelerate. And here, in its most basic form, is how it works. Based upon my experience and results, the key to successful improvement initiatives is focusing your improvement efforts on the right area, the system constraint.
Both Six Sigma and Lean are absolutely necessary for business improvement… the only difference being where and when to apply them. Keep in mind that all problems are not created equal, so the type of tool or action required and the order in which they are applied could be different depending upon the scenario.